What is the difference between EN 388 and ANSI/ISEA?
When choosing protective gloves, it is crucial to understand the various standards that apply to ensure the best possible protection against injuries. Two of the most recognized standards are the European EN 388 standard and the American ANSI/ISEA 105 standard. These standards have different approaches and methods for testing and classifying glove materials, which can affect which gloves are best suited for specific work conditions.
RESISTANCE TO ABRASION
The American standard ANSI/ISEA 105-2016 for abrasion testing evaluates how many cycles are required for an abrasion wheel to break down the glove material. For levels 0 to 3, a load of 500 grams is applied to the abrasion wheel, while levels 4 to 6 use a load of 1000 grams. The glove material is mounted and abraded by the rotating wheel until a hole form under the corresponding weight. The more cycles it takes for the material to break down, the higher the abrasion rating. The classification level is reported as an average of at least five samples.
The results are shown in the table below.














In the European standard EN388, circular samples of the material are tested under a constant pressure of (9.0 ± 0.2) kPa, approximately 435g weight load. The resistance to abrasion is measured by the number of rubs required for breakthrough. Four samples should be taken from four different gloves of the same glove series. The performance level is defined as the lowest of the four values.
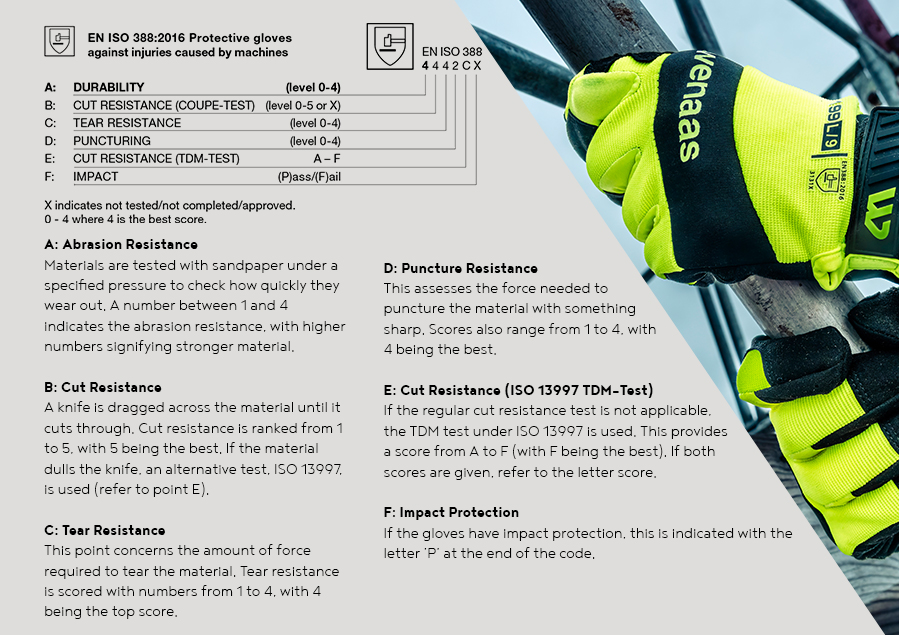
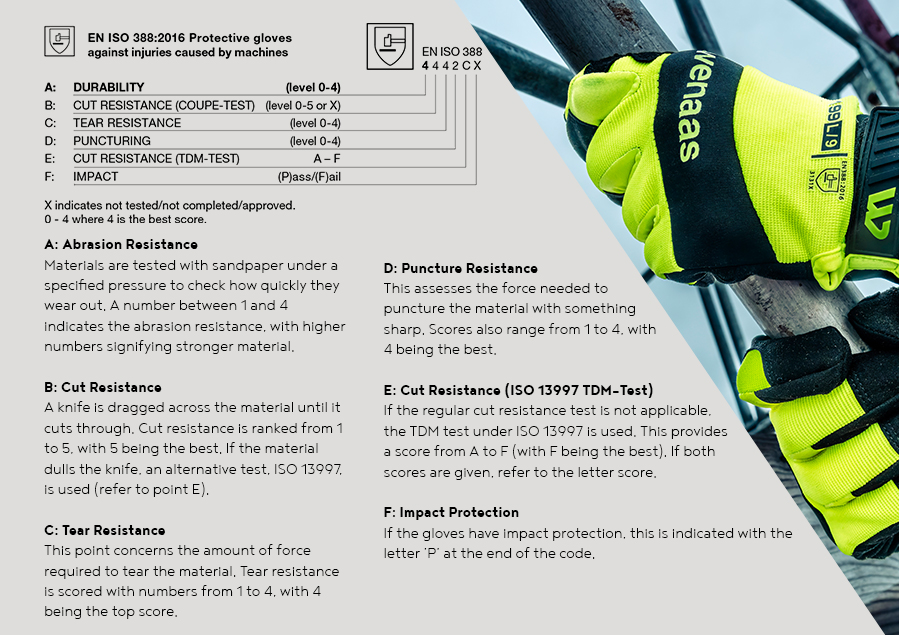
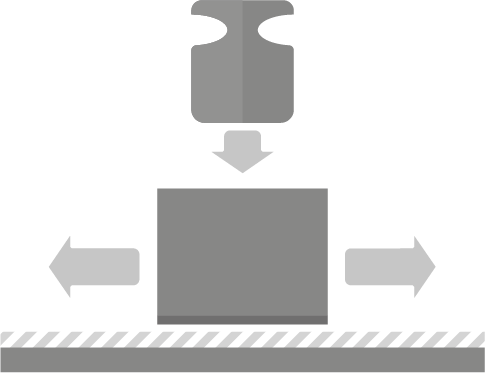
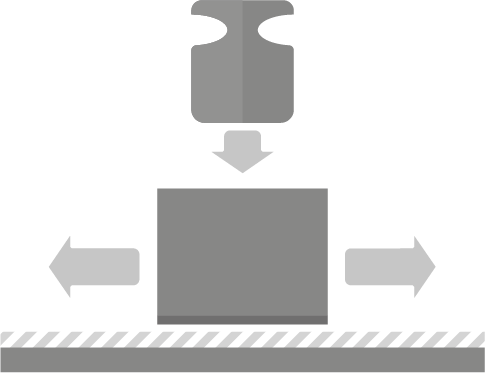
EN 388 Abrasion Test
The material from the palm of the glove is placed in a machine that uses standardized abrasive paper. The paper is rubbed against the material until a hole forms. There are significant differences between the levels, with level 1 corresponding to 100 rubs and level 4 corresponding to 8000 rubs. The results are shown in the table below.
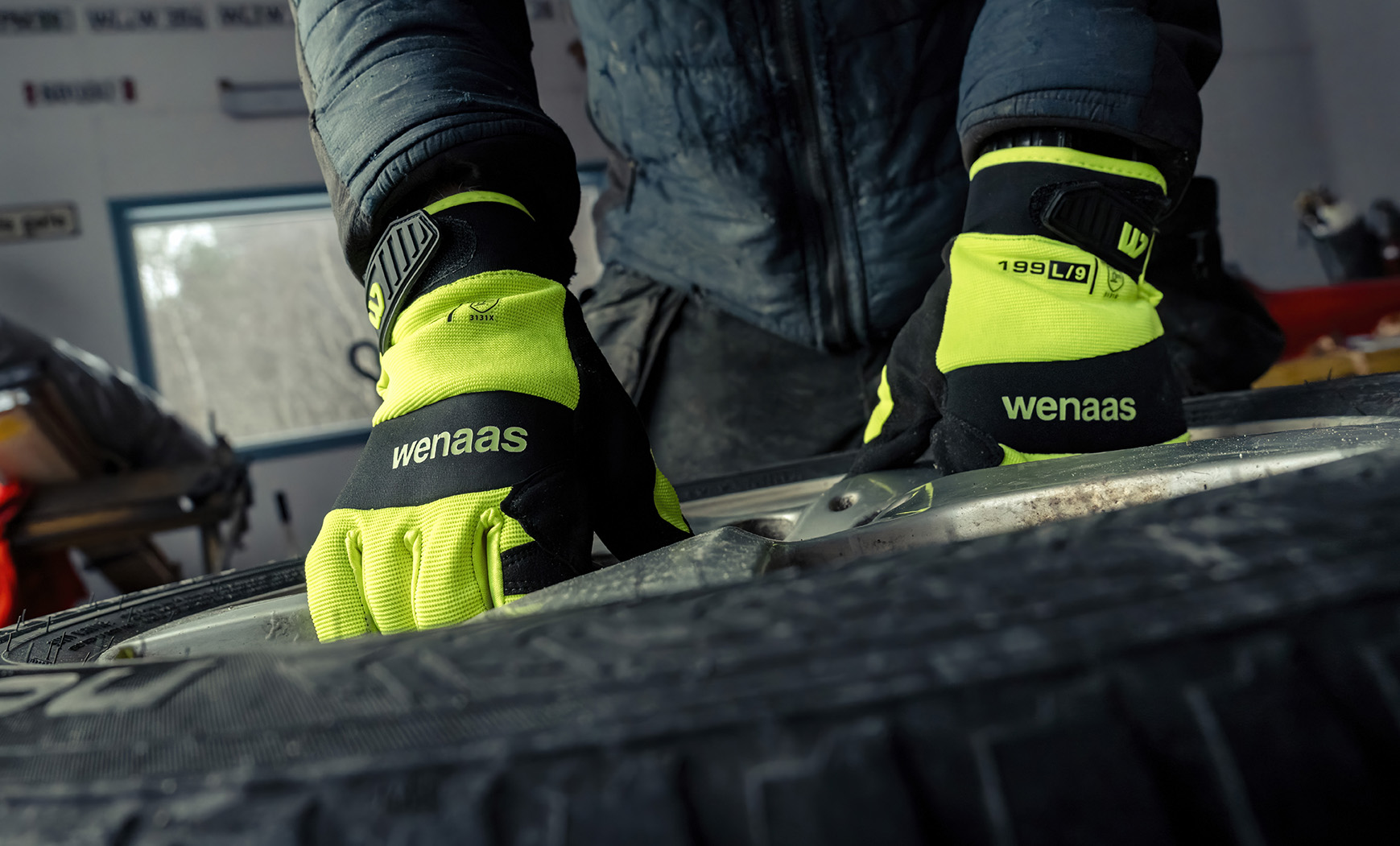
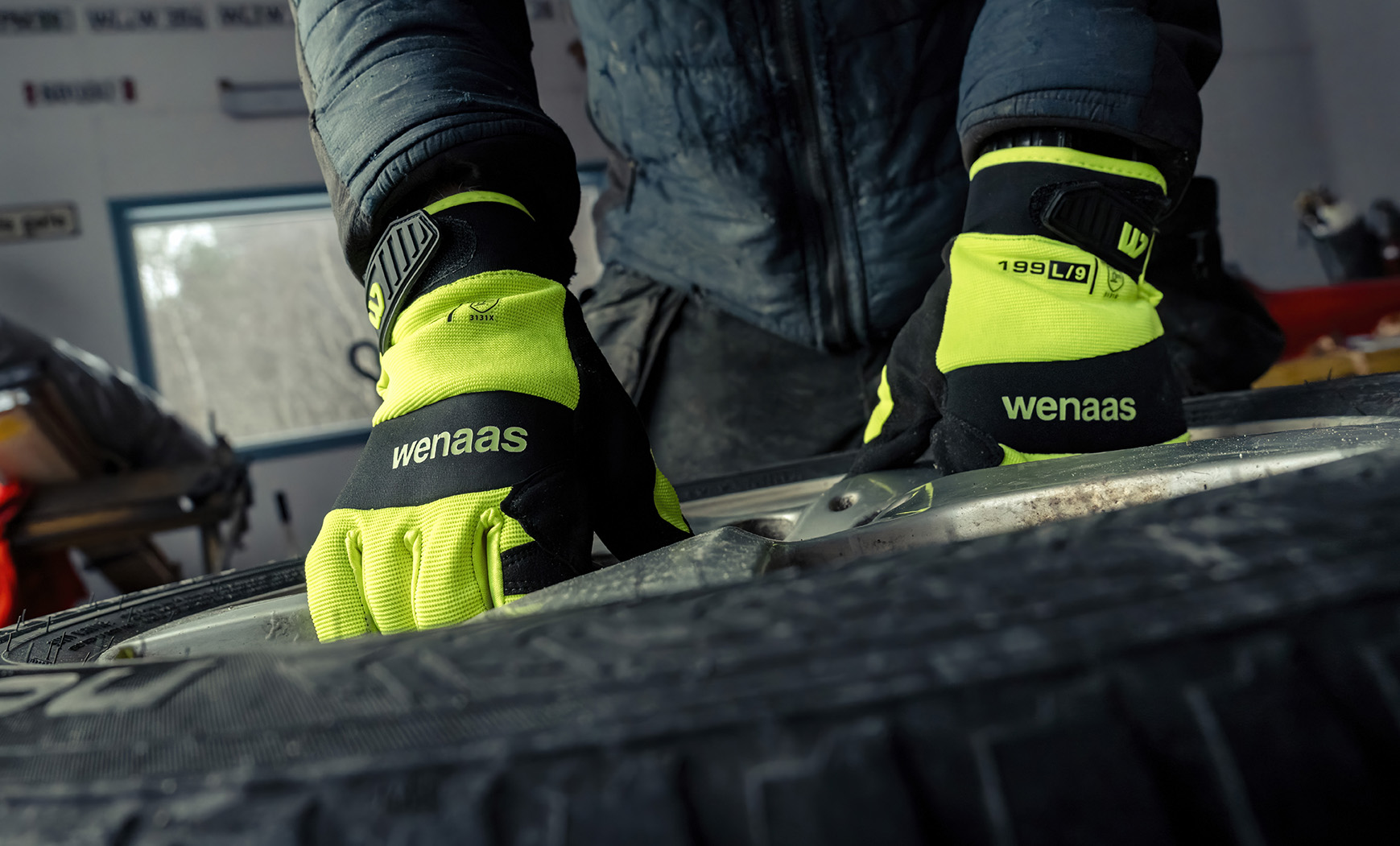


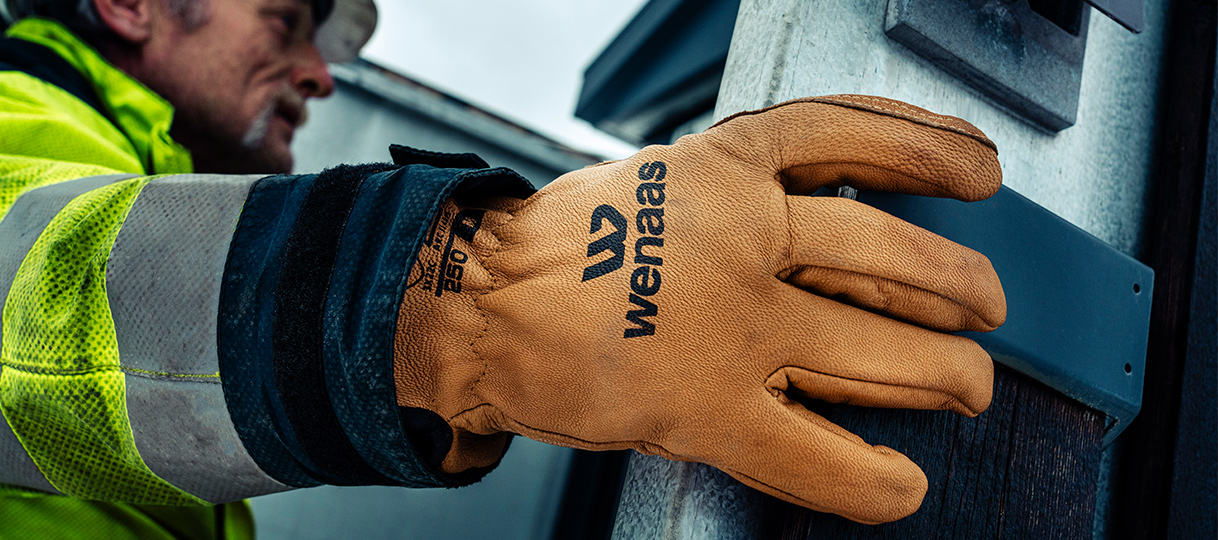
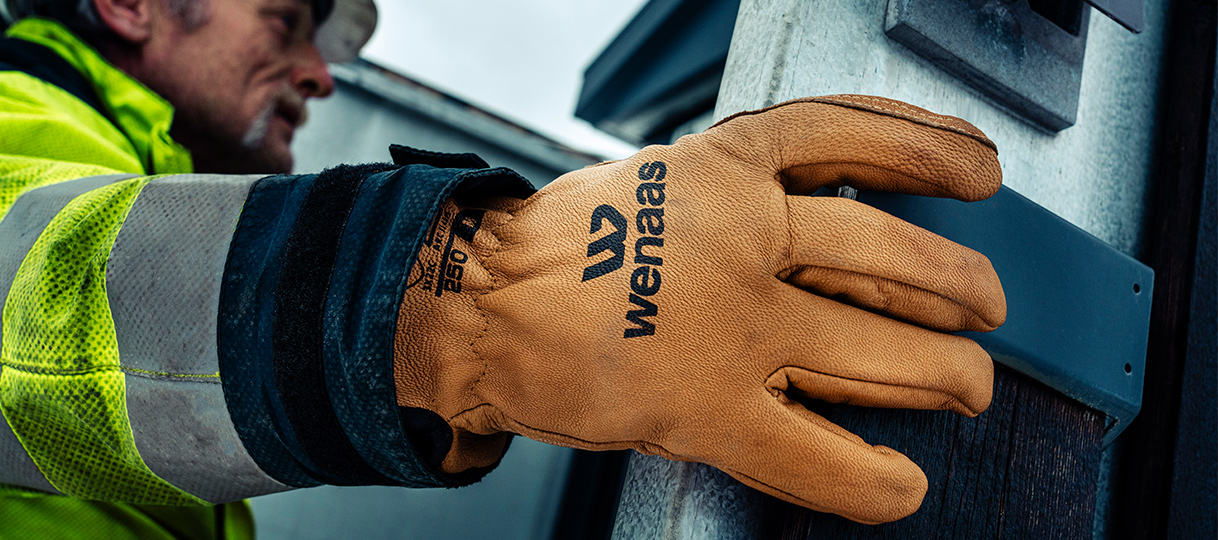
RESISTANCE TO CUTS
When choosing work gloves that protect against cuts, it can be helpful to understand both the European and American classification systems for cut resistance, as many gloves will display both markings. It is important to remember that due to different testing methods, ANSI and EN 388 cut resistance results do not always match based on cut load. Work gloves that protect against cuts have a tight fit, high abrasion resistance, and are often made from knitted material that contains fiberglass.
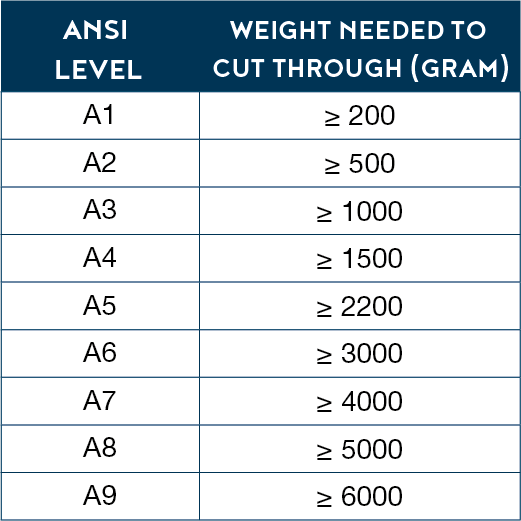
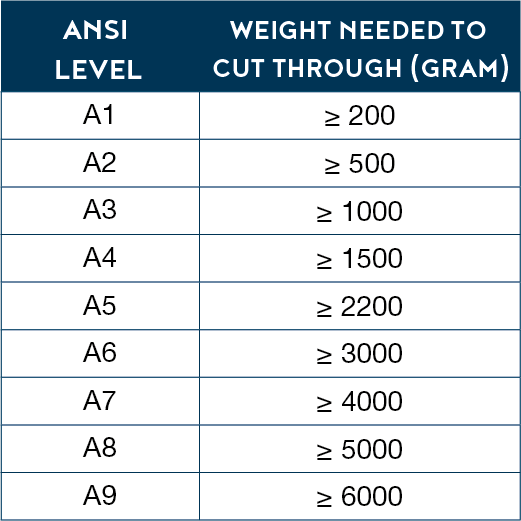
In the USA, the ANSI/ISEA 105 standard includes a test with a scale of 9 levels of cut resistance, A1-A9. The levels indicate how many grams are required to cut through a sample using a rectangular blade in the specified cut test machine.


















The European standard includes two different tests: the TDM-100 test (the same machine used by ANSI), where the levels (A-F) indicate the force in newtons (N) required to cut through a sample using a rectangular blade in the cut test machine. This test is optional unless the blade in the Coupe test becomes dull, in which case it becomes the reference for cut resistance. The Coupe test is more complex. A glove is assigned a cut level from 0 to 5 (where 5 is the most resistant to cuts) based on the material's "cut index." The cut index is a ratio that compares the material's cut resistance to the cut resistance of a reference cotton fabric.
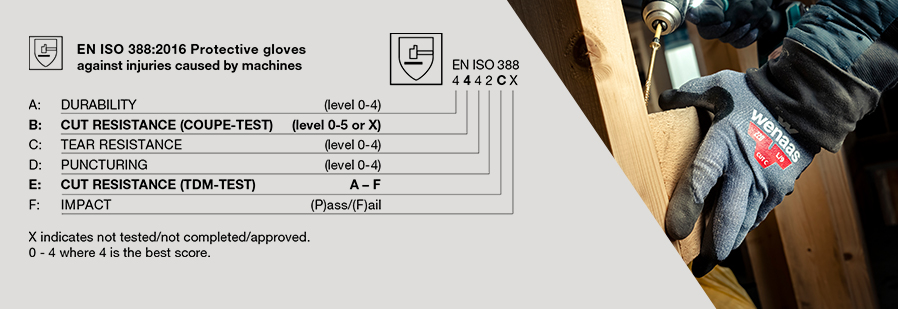
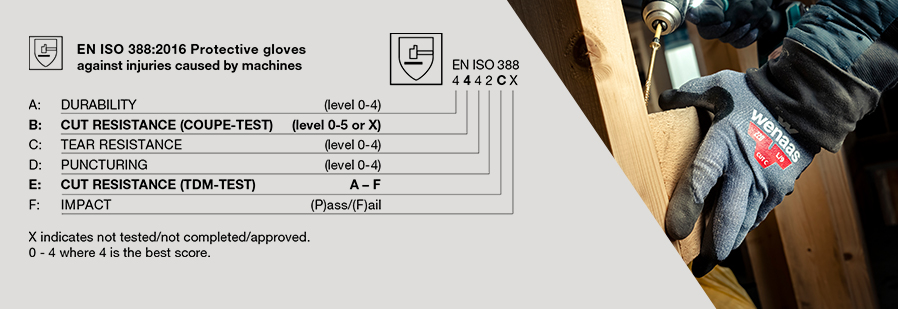
Coupe test
A circular blade rotates on the glove material while moving back and forth at a constant speed and pressure until the blade cuts through. The result is compared with the reference material, and an index is calculated.
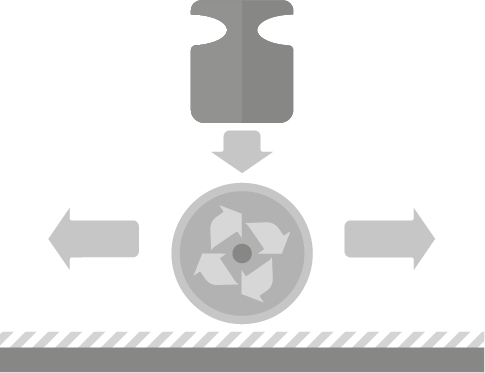
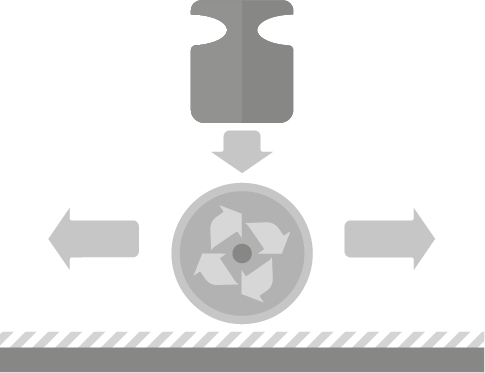
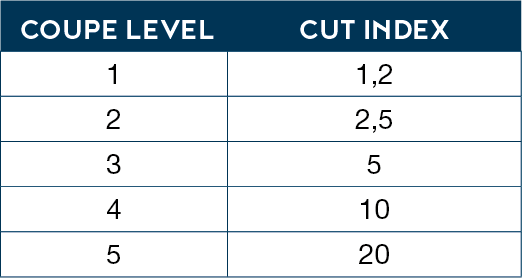
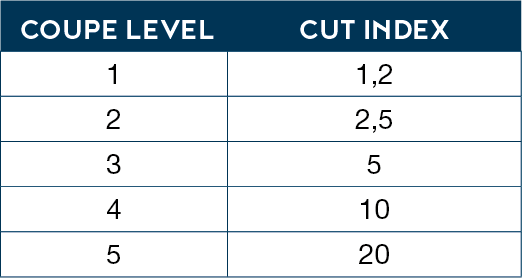
TDM test
This straight blade test is used when the circular blade test cannot be applied. The straight blade test measures the applied vertical force and the distance required to cut through the glove with the standardized blade. After each cut on the sample, a new blade is used, and the force increases the performance level, which is rated from A to F, with F being the highest level of cut resistance.
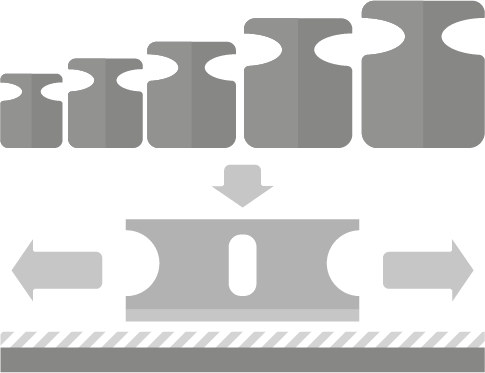
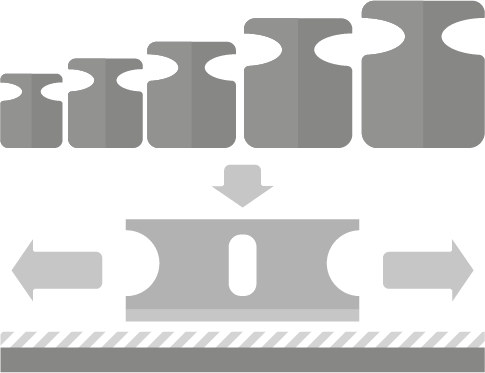
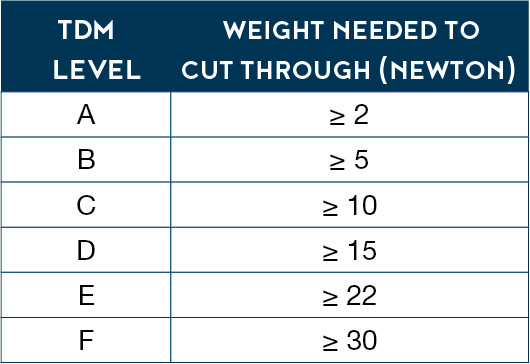
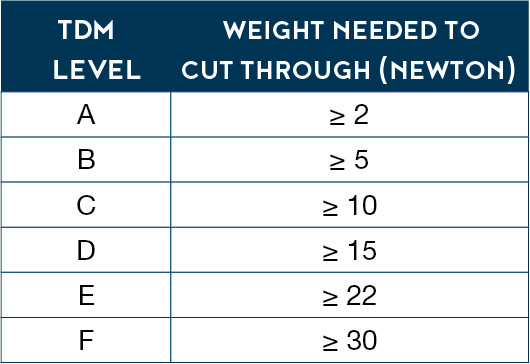
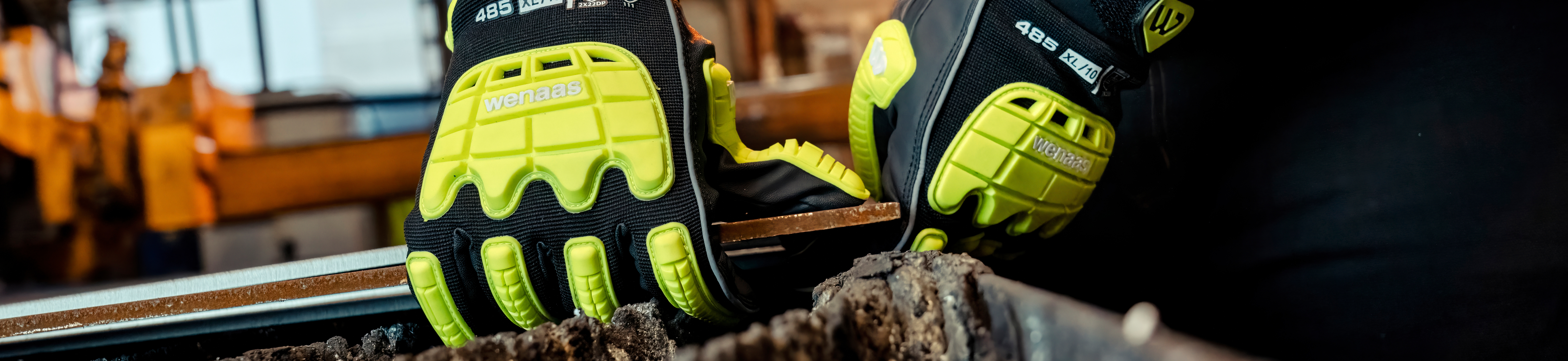
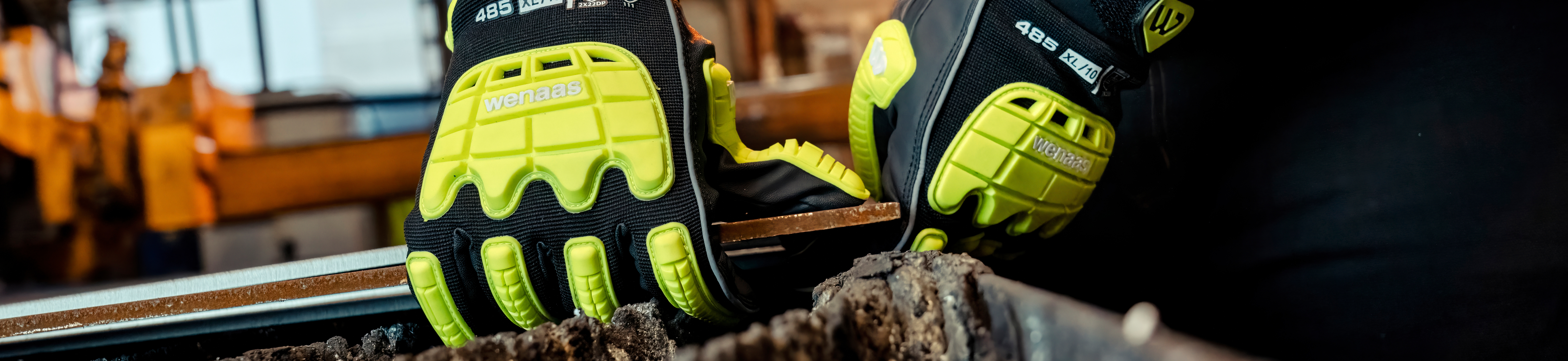
IMPACT RESISTANCE
When choosing a work glove that protects against crush injuries, impact injuries, and similar hazards, the two global standards EN 388 and ANSI/ISEA 138 apply. Both standards have similar test methods where a weight is dropped on the impact-prone areas with an energy of 5 Joules. The difference lies in the scoring and evaluation systems.
The American standard requires gloves designed to protect the knuckles and fingers from impact forces. Impact resistance is classified into 3 levels (1-3), with level 1 providing the lowest protection and level 3 the highest. The areas tested include the knuckles on the back of the hand, fingers, and thumb. The lowest performance value sets the overall protection level.








EN 388 only tests impact on the knuckles, back, or palm, where 4 different gloves are tested. Fingers are not tested. The EN 388 test is given a simple pass (P) or fail (F). X indicates not tested/not applicable/approved. To pass, the average transmitted force from the 4 tested gloves must be less than or equal to 7 kN, with no individual results greater than 9 kN.
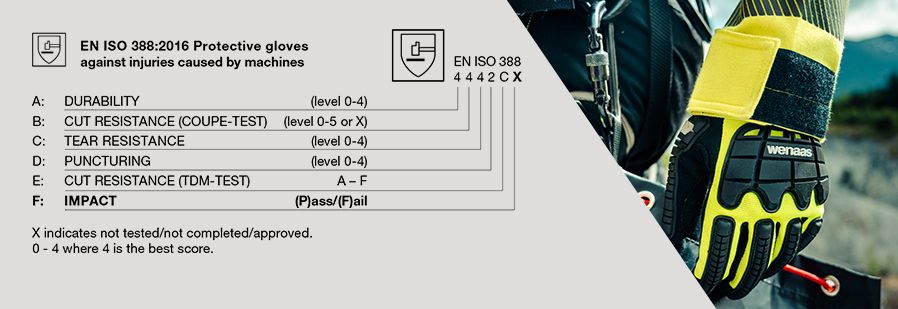
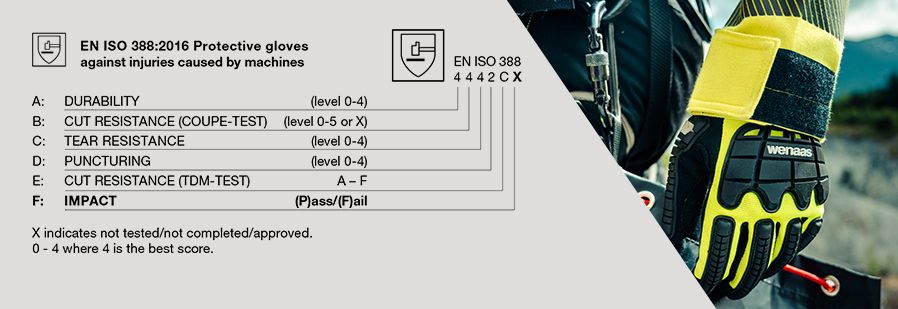
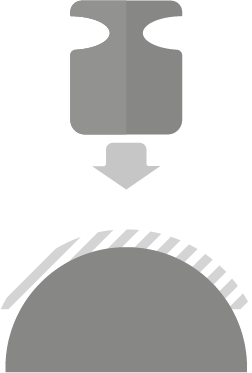
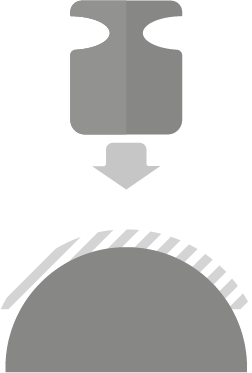


The material is placed over a domed anvil, a weight with an impact energy of 5 Joules is dropped on the material, and the transmitted force is measured. If the glove has sufficient impact protection, the letter P will be displayed. This test is only used on gloves with impact resistance properties.